Испытания и классы герметичности трубопроводной арматуры
В процессе изготовления трубопроводной арматуры могут иметь место дефекты материала деталей или погрешности обработки и сборки, которые снижают прочность конструкции или ухудшают эксплуатационные качества изделия. Для выявления этих дефектов и последующей их ликвидации арматура проходит гидравлическое испытание, которое выполняется в два этапа:
- гидравлическое испытание изделия на прочность, непроницаемость металла, неподвижных разъемных соединений и сальника - испытание на прочность;
- испытание рабочего (запорного) органа изделия на герметичность - испытание на герметичность.
Детали арматуры, изготовляемые отливкой, могут иметь такие дефекты, как песчаные (земляные) и газовые раковины, пористость («рыхлота») металла, трещины, разностенность в результате смещения стержня в литейной форме, остаточные внутренние напряжения. В сварных соединениях возможны непровар, трещины, пористость, смещение стенок, растрескивание околошовной зоны.
Для того, чтобы гарантировать прочность металла, производят испытание на прочность. Испытание проводят при пробном давлении, установленном ГОСТ 356-80, которое в 1,25÷2 раза превышает условное давление. Испытание проводится водой при нормальной температуре, а наличие или отсутствие протечек выявляется внешним осмотром испытуемого изделия по падению давления в замкнутом объеме или соответствующими приборами. Гидравлическое испытание должно производиться до окраски изделия. Давление обычно создается при помощи насосов. Применять при высоких давлениях воздух, другие газы или пар для этих целей не рекомендуется, так как опасно для персонала, поскольку испытанию подлежат изделия, прочнось которых окончательно еще не установлена. Продолжительность испытания устанавливается соответствующей технической документацией (стандартами или техническими условиями). Время выдержки изделия под пробным давлением должно быть достаточным для осмотра и установления годности изделия. В ряде случаев, продолжительность нахождения под давлением принимается в зависимости от наибольшей толщины стенки корпусных деталей. Для ответственных изделий выдержка принимается не менее 10 минут. После выдержки давление снижают до 4/5 пробного давления и производят тщательный осмотр изделия. Давление при осмотре должно поддерживаться постоянным. Пропуск воды и потение через металл в сварные швы не допускаются.
Испытанию должны подвергаться все полости арматуры, заполняемые рабочей средой, поэтому арматура испытывается при открытом положении запорного органа, но с заглушенными проходными отверстиями. Литые детали при испытании на прочность простукиваются свинцовым или медным молотком массой 0,8÷1,0 кг. Детали, в которых при испытаниях выявлены течь или потение, после исправления заваркой должны быть подвергнуты повторному испытанию.
В целях предохранения внутренних поверхностей корпусных деталей от коррозии, для испытания иногда используется 5% водный раствор моющего препарата.
Испытание на герметичность проводится для проверки качества пригонки (притирки) уплотнительных поверхностей деталей запорного органа арматуры. Одновременно контролируется качество сборки разъемных соединений. Гидравлическое испытание на герметичность производится под условным давлением ру и выполняется после гидравлического испытания на прочность. При испытаниях затворов фланцевых, задвижек стальных и кранов давление создается с каждой из сторон запорного органа – сначала с одной, а затем с другой стороны. Соответственно, с противоположной стороны производится осмотр. В вентилях, клапанах и заслонках испытание производится, как правило, с одной стороны. Энергетическая арматура изготовляется и испытывается по особым техническим условиям. Арматура, снабженная приводами, дополнительно испытывается на герметичность перекрытия запорного органа приводом.
В закрытом положении запорная арматура не должна пропускать среду из одной части трубопровода в другую, отделенную запорным органом. Однако, в ряде случаев, нет необходимости предъявлять к арматуре особо высокие требования в отношении герметичности, поскольку иногда некоторая незначительная протечка среды допустима, а обеспечение абсолютной герметичности запорного органа бывает сложным и экономически неоправданным. В связи с этим разработана классификация арматуры по классам герметичности с соответствующими нормами допустимой протечки, предусмотренными ГОСТ 9544.
Класс герметичности устанавливается в зависимости от назначения арматуры:
- 1-й класс - арматура для взрывоопасных и токсичных сред;
- 2-й класс - арматура для пожароопасных сред;
- 3-й класс - арматура для остальных сред.
Сделать заказ
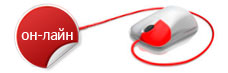
1. При заказе ручной (рукоятка, редуктор) арматуры (без привода) заполняется электронная заявка.
2. В случае заказа приводной арматуры, необходимо заполнить опросный лист и направить его на электронную почту: zakaz@metarossa.ru